Trong lĩnh vực lọc dầu, biên độ lợi nhuận luôn là bài toán nan giải của bất cứ nhà máy nào. Nhà máy Lọc dầu (NMLD) Dung Quất đã trải qua 7 năm vận hành thương mại và nay đứng trước bài toán: Làm thế nào để nâng cao hiệu quả, tăng lợi nhuận? Các kỹ sư giỏi của Công ty Lọc hóa dầu Bình Sơn (BSR) đã có nhiều sáng kiến, giải pháp kỹ thuật nhằm đạt được sự kỳ vọng đó.
Công ty đã tiết kiệm được 481 tỉ đồng; trong đó giảm tiêu hao trong chế biến, tối ưu hóa năng lượng nội bộ đạt 346 tỉ đồng chỉ tính trong 10 tháng. Các tiết kiệm khác như tự thực hiện bảo dưỡng sửa chữa, tiết giảm chi phí… đạt 123 tỉ đồng. Riêng tiêu thụ năng lượng nội bộ của nhà máy theo định mức được phê duyệt là 7,6%. Nhưng thực tế đạt được là 7,33%; Tiết kiệm 127,68 tỉ đồng.
Tiết kiệm năng lượng
BSR phối hợp với Hãng Solomon nhằm đánh giá giá trị nhân lực, vật lực, năng lượng của NMLD Dung Quất đang ở đâu so với 400 nhà máy lọc dầu trên thế giới. Sau một thời gian hợp tác, Solomon đưa ra hàng loạt các thông tin hữu ích về nhà máy để các bộ phận chuyên môn BSR nghiên cứu, tìm giải pháp khắc phục. Sau đó, Hãng Shell Global dựa trên những phân tích của Solomon tiếp tục khuyến nghị BSR những giải pháp kỹ thuật để năng cao hiệu quả chế biến của nhà máy. Shell Global đề xuất 34 giải pháp vận hành và nhóm các giải pháp có cải hoán. Kỹ sư Ngô Đức Khánh cho biết thêm, Phòng Kỹ thuật đã sàng lọc ra 17 giải pháp để đưa vào áp dụng tại các phân xưởng của nhà máy. Trong đó có những giải pháp đạt hiệu quả kinh tế cao như: Giảm tỷ lệ hồi lưu tháp NHT Splitter T1202, giảm tỷ lệ tuần hoàn hydro (H2:Oil) ở phân xưởng CCR (giai đoạn 1), giảm áp suất đầu ra máy nén MAB, giảm tiêu thụ MPS tại thiết bị phản ứng của phân xưởng RFCC, hạn chế xả đuốc ở D2401… Hiện có 11 giải pháp đã được áp dụng, mỗi tháng tiết kiệm cho công ty khoảng 3,6 tỉ đồng.
Trong những giải pháp ấy, giảm tỷ lệ hồi lưu tháp NHT Splitter T1202 chiếm 1,86 tỉ đồng/tháng - là giải pháp có giá trị cao nhất. Tháp phân tách Naphtha T-1202 (thuộc Phân xưởng Naphtha Hydro Treating - unit 012) được thiết kế để phân tách toàn bộ dãy naphtha đã được xử lý thành naphtha nhẹ (nguyên liệu cho phân xưởng ISOM) và naphtha nặng (nguyên liêu cho phân xưởng CCR).
Theo đó, hiệu quả phân tách của tháp sẽ cao khi tăng tỷ lệ tuần hoàn hồi lưu đỉnh tháp và nguyên liệu đi vào tháp (tỷ lệ giữa R/F). Như vậy, việc điều chỉnh tối ưu tỷ lệ R/F này mang lại lợi ích tối ưu công suất của thiết bị đun sôi lại ở đáy tháp và thiết bị ngưng tụ dòng đỉnh tháp.
Để đảm bảo việc triển khai quá trình thử nghiệm, Phòng Kỹ thuật đã tiến hành chạy mô phỏng dựa trên điều kiện nguyên liệu hiện tại nhằm đánh giá và xác định khoảng tỷ lệ R/F tối ưu đảm bảo duy trì ổn định vận hành và chất lượng sản phẩm vẫn đạt tiêu chuẩn cho phép (dãy hoạt động tối ưu cho tỷ lệ R/F đã được xác định từ 1.0 xuống 0.5m3/m3). Quá trình thực hiện việc chạy thử được tiến hành theo đúng quy trình, đảm bảo việc kiểm soát chặt chẽ và an toàn ổn định theo từng bước. Giảm dần tỷ lệ từ 1,0 xuống 0,5 (với bước điều chỉnh giảm là 0,1). Tại mỗi bước điều chỉnh giảm đều được giữ ổn định trong 1-2 ngày để kiểm tra và đánh giá đảm bảo sản phẩm vẫn đạt tiêu chuẩn chất lượng.
Thời gian triển khai việc thử nghiệm thực tế tại phân xưởng được tiến hành từ ngày 23-5-2016 đến ngày 3-6-2016 và được duy trì trong 2 tuần tiếp theo đến hết ngày 17-6-2016 để đánh giá tổng thể giải pháp và thu thập số liệu. Quá trình thử nghiệm đã đạt thành công khi tỷ lệ R/F đã được tối giảm xuống 0.5-0.6m3/m3 với kết quả tiết kiệm năng lượng tiêu thụ đạt lượng hơi trung áp (hơi MP steam) đã tiết giảm được từ 6-8 tấn/giờ; lượng điện tiêu thụ đã tiết giảm được 38-58kW/giờ.
Giải pháp giảm áp suất đầu ra của máy nén Main Air Blower (MAB) tại Phân xưởng Cracking xúc tác (RFCC) nhằm tiết giảm tiêu thụ hơi cao áp (HPS) tại turbine hơi của MAB cũng là một sáng kiến hay của các kỹ sư BSR. Máy nén MAB được sử dụng để cung cấp không khí đốt cốc trong thiết bị tái sinh xúc tác. Áp suất vận hành bình thường ở đầu ra của MAB là 3kg/cm2g và giá trị cài đặt cảnh báo áp suất thấp là 2,9kg/cm2g.
Dựa trên vận hành thực tế, áp suất đầu ra của MAB được đánh giá có thể duy trì thấp hơn giá trị thiết kế để tiết kiệm năng lượng thông qua việc giảm tiêu thụ hơi nước cao áp. Theo thông lệ vận hành, áp suất đầu ra MAB được duy trì cao hơn áp ở thiết bị sử dụng khoảng 0,5-0,8kg/cm2g để đảm bảo độ mở của van điều khiển trên các nhánh khí ở hạ nguồn nằm trong giới hạn chuẩn.
Đề xuất giảm đầu ra của MAB từ 3kg/cm2g xuống 2,8kg/cm2g đã được phê duyệt từ đầu tháng 6-2015. Từ 30-6-2015, kỹ sư vận hành hiện trường bắt đầu cho giảm áp đầu ra MAB xuống 2,9 kg/cm2g và duy trì ở mức đó 10 ngày. Sau đó tiếp tục giảm còn 2,85kg/cm2g.
Thật bất ngờ, lượng không khí cung cấp cho các đơn vị vẫn được duy trì ở mức cho phép. Ở điều kiện này, độ mở của các van điều khiển trên các nhánh ra của MAB vẫn nằm trong giới hạn vận hành tối ưu (20-80%) của các van. Các thông số tiêu thụ hơi ở turbine hơi MAB giảm. Tính ra lượng hơi HP tiết giảm được là 11.377 tấn. MAN TURBO đã kiểm tra đường đặc tính của MAB và xác nhận điểm vận hành hiện tại của MAB vẫn còn xa ngưỡng cho phép của máy nén.
Theo quan điểm của nhà bản quyền công nghệ Axens (Pháp) cho rằng, không có yêu cầu đặc biệt phải kiểm soát áp suất đầu ra của MAB ở giá trị 3kg/cm2g. Sự vận hành của MAB nói chung và sự cài đặt áp suất đầu ra phải đảm bảo cung cấp đủ lưu lượng và áp suất không khí theo yêu cầu của các đơn vị sử dụng với mức dư hợp lý. Tính đến ngày 21-4-2016 (287 ngày) thì lợi nhuận đạt được là 11.377 tấn HP, ước lượng tương đương khoảng 246.000USD.
Tối ưu hóa công suất vận hành
Năm 2016, một trong những yếu tố thành công là NMLD Dung Quất luôn hoạt động an toàn, ổn định ở 105% công suất thiết kế. Công suất của nhà máy là 6,5 triệu tấn dầu thô nhưng BSR sản xuất khoảng 6,91 triệu tấn sản phẩm, vượt thiết kế 0,41 triệu tấn. Đó là thành quả của 5% công suất vượt.
Kỹ sư Đặng Ngọc Đình Điệp, Phó trưởng phòng Kỹ thuật BSR cho biết: Nếu tăng công suất của Phân xưởng Chưng cất dầu thô (CDU) lên cao hơn so với 100% công suất và điều chỉnh dải công suất của các phân xưởng phía sau một cách phù hợp sẽ giúp tăng thêm lợi nhuận vì khi công suất nhà máy tăng thêm khoảng 10-15% thì các chi phí cố định thay đổi không đáng kể. “Việc thay đổi công suất cao hơn thiết kế đòi hỏi phải tính toán và xem xét giới hạn của các điều kiện vận hành, đánh giá lại toàn bộ các thiết bị, hệ thống. Như vậy, cần phải có nghiên cứu tổng thể nhằm tối ưu công suất nhà máy”.
Nghiên cứu khả năng tối đa công suất NMLD Dung Quất được bắt đầu bằng việc nghiên cứu các dữ liệu như tài liệu thiết kế nhà máy; số liệu vận hành thực tế của nhà máy; kết quả nghiên cứu cho dự án nâng cấp mở rộng nhà máy; tính chất và thành phần dầu thô đưa vào chế biến.
Từ các nghiên cứu ban đầu, BSR đã xác định được giới hạn cho việc tăng công suất của nhà máy nằm ở Phân xưởng CDU. Để đánh giá khả năng tăng công suất của phân xưởng này, một mô hình mô phỏng nhiệt động học đã được xây dựng và sử dụng kết hợp với các số liệu chạy thử nghiệm để đánh giá chi tiết cân bằng vật chất, cân bằng nhiệt cũng như hoạt động của các thiết bị khi công suất phân xưởng tăng lên.
Trong NMLD Dung Quất, hệ thống thiết bị đã được thiết kế với giới hạn dư tối thiểu là 10% (design margin); một số thiết bị quan trọng như quạt thổi khí, máy nén khí… có giới hạn dư lên tới 10-25%. Tuy nhiên, thực tế dầu thô chế biến có sự khác biệt rất lớn so với dầu thô thiết kế (tỷ lệ thành phần các phân đoạn thay đổi lớn theo hướng nhiều phân đoạn khí nhẹ, nhiều phân đoạn naphtha, nhiều DO, ít phân đoạn cặn residue…). Vì vậy, việc đánh giá, nghiên cứu bằng mô hình được thực hiện với 3 loại hỗn hợp dầu khác nhau: Hỗn hợp dầu thô đặc trưng; Hỗn hợp dầu có hiệu suất phân đoạn naphtha cao; Hỗn hợp dầu có hiệu suất phân đoạn DO cao đóng vai trò quan trọng trong việc nghiên cứu tăng công suất nhà máy.
Sự mạnh dạn áp dụng giải pháp này căn cứ vào 2 thực tiễn đã được chứng minh. Căn cứ kết quả nghiên cứu của Hãng JGC (Nhật Bản) cho Dự án nâng cấp mở rộng NMLD Dung Quất cho thấy, khi tăng công suất 10-15% so với giá trị thiết kế, toàn bộ các phân xưởng công nghệ, phụ trợ, ngoại vi đều không đòi hỏi phải cải hoán hoặc yêu cầu cải hoán nhỏ. Ngoài ra, trong khoảng thời gian từ 11-2010 đến 10-2012, NMLD Dung Quất đã vận hành an toàn, ổn định và liên tục ở công suất 105% so với công suất thiết kế với nhiều hỗn hợp dầu thô khác nhau.
Phân xưởng CDU được đánh giá là giới hạn chính khi nâng công suất nhà máy lên 110%. Các kỹ sư đã thực hiện quy trình tăng công suất phân xưởng CDU lần lượt phân tích số liệu; Chạy thử nghiệm ở 100% công suất. Bước tiếp theo là thực hiện chạy thử nghiệm ở 110% công suất. Cuối năm 2013, Phân xưởng CDU được chạy thử nghiệm nâng công suất từ 100 lên 110% với các điều kiện được điều chỉnh nhằm giảm bớt các giới hạn có thể ảnh hưởng đến việc tăng công suất như: Giới hạn công suất bên trong cột chưng cất dầu thô, đặc biệt vùng bơm tuần hoàn LGO và HGO; công suất lò gia nhiệt dầu thô; giới hạn công suất của các bơm tuần hoàn; công suất của tháp ổn định xăng thô, đặc biệt thiết bị tái đun sôi tại đáy tháp. Việc chạy thử nghiệm đã thành công ở 110% công suất, các sản phẩm đều đạt tiêu chuẩn đặt ra, các thiết bị hoạt động trong giới hạn an toàn.
Nhằm xem xét và đánh giá chính xác hoạt động của Phân xưởng CDU trong giai đoạn chạy thử nghiệm, mô hình mô phỏng công nghệ và thiết bị đã được xây dựng và tinh chỉnh theo các thông số vận hành đã thu thập được. Nguyên liệu cho mô phỏng được tổng hợp bằng cách phối trộn các sản phẩm của phân xưởng CDU. Còn đối với dầu thải, do phối trộn với một lượng nhỏ nên tính chất được giả thiết nhằm đảm bảo cân bằng vật chất. Kết quả mô phỏng thu được rất gần với điều kiện thực nên đáng tin cậy khi sử dụng để đánh giá.
Trên cơ sở thông tin từ chạy thử nghiệm ngày 25-12-2014 và trên cơ sở tính toán thực hiện bởi mô phỏng với hỗn hợp dầu thô đặc trưng, có thể xác nhận được từng thiết bị như lò gia nhiệt dầu thô, các thiết bị tĩnh, đĩa trong tháp chưng cất dầu thô, các thiết bị trao đổi nhiệt, các thiết bị làm mát bằng không khí, các thiết bị quay và các thiết bị điều khiển… đều có khả năng vận hành ở 110% công suất.
Tuy nhiên, nhằm tăng độ linh động và sự ổn định cần thiết khi chế biến ở 110% công suất cần có thêm một số cải hoán nhỏ: lắp thêm đường thu hồi khí ở phân xưởng CDU, lắp đặt thêm thiết bị tái đun sôi ở đáy tháp ổn định xăng naphtha T-1107, xem xét thay thế một số van điều khiển có kích thước lớn hơn, xem xét tăng độ nghiêng cánh quạt của các thiết bị làm mát bằng không khí, tăng tần suất làm sạch các thiết bị trao đổi nhiệt để tăng khả năng thu hồi nhiệt cho dầu thô.
Công ty đã tiết kiệm được 481 tỉ đồng; trong đó giảm tiêu hao trong chế biến, tối ưu hóa năng lượng nội bộ đạt 346 tỉ đồng chỉ tính trong 10 tháng. Các tiết kiệm khác như tự thực hiện bảo dưỡng sửa chữa, tiết giảm chi phí… đạt 123 tỉ đồng. Riêng tiêu thụ năng lượng nội bộ của nhà máy theo định mức được phê duyệt là 7,6%. Nhưng thực tế đạt được là 7,33%; Tiết kiệm 127,68 tỉ đồng.
Tiết kiệm năng lượng
BSR phối hợp với Hãng Solomon nhằm đánh giá giá trị nhân lực, vật lực, năng lượng của NMLD Dung Quất đang ở đâu so với 400 nhà máy lọc dầu trên thế giới. Sau một thời gian hợp tác, Solomon đưa ra hàng loạt các thông tin hữu ích về nhà máy để các bộ phận chuyên môn BSR nghiên cứu, tìm giải pháp khắc phục. Sau đó, Hãng Shell Global dựa trên những phân tích của Solomon tiếp tục khuyến nghị BSR những giải pháp kỹ thuật để năng cao hiệu quả chế biến của nhà máy. Shell Global đề xuất 34 giải pháp vận hành và nhóm các giải pháp có cải hoán. Kỹ sư Ngô Đức Khánh cho biết thêm, Phòng Kỹ thuật đã sàng lọc ra 17 giải pháp để đưa vào áp dụng tại các phân xưởng của nhà máy. Trong đó có những giải pháp đạt hiệu quả kinh tế cao như: Giảm tỷ lệ hồi lưu tháp NHT Splitter T1202, giảm tỷ lệ tuần hoàn hydro (H2:Oil) ở phân xưởng CCR (giai đoạn 1), giảm áp suất đầu ra máy nén MAB, giảm tiêu thụ MPS tại thiết bị phản ứng của phân xưởng RFCC, hạn chế xả đuốc ở D2401… Hiện có 11 giải pháp đã được áp dụng, mỗi tháng tiết kiệm cho công ty khoảng 3,6 tỉ đồng.
Trong những giải pháp ấy, giảm tỷ lệ hồi lưu tháp NHT Splitter T1202 chiếm 1,86 tỉ đồng/tháng - là giải pháp có giá trị cao nhất. Tháp phân tách Naphtha T-1202 (thuộc Phân xưởng Naphtha Hydro Treating - unit 012) được thiết kế để phân tách toàn bộ dãy naphtha đã được xử lý thành naphtha nhẹ (nguyên liệu cho phân xưởng ISOM) và naphtha nặng (nguyên liêu cho phân xưởng CCR).
Theo đó, hiệu quả phân tách của tháp sẽ cao khi tăng tỷ lệ tuần hoàn hồi lưu đỉnh tháp và nguyên liệu đi vào tháp (tỷ lệ giữa R/F). Như vậy, việc điều chỉnh tối ưu tỷ lệ R/F này mang lại lợi ích tối ưu công suất của thiết bị đun sôi lại ở đáy tháp và thiết bị ngưng tụ dòng đỉnh tháp.
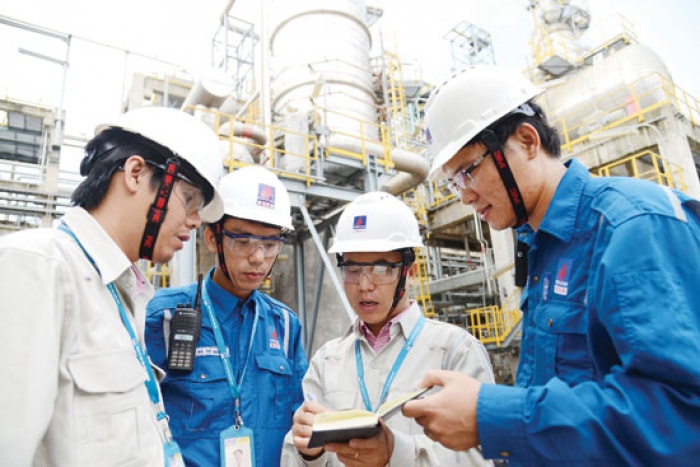
Thời gian triển khai việc thử nghiệm thực tế tại phân xưởng được tiến hành từ ngày 23-5-2016 đến ngày 3-6-2016 và được duy trì trong 2 tuần tiếp theo đến hết ngày 17-6-2016 để đánh giá tổng thể giải pháp và thu thập số liệu. Quá trình thử nghiệm đã đạt thành công khi tỷ lệ R/F đã được tối giảm xuống 0.5-0.6m3/m3 với kết quả tiết kiệm năng lượng tiêu thụ đạt lượng hơi trung áp (hơi MP steam) đã tiết giảm được từ 6-8 tấn/giờ; lượng điện tiêu thụ đã tiết giảm được 38-58kW/giờ.
Giải pháp giảm áp suất đầu ra của máy nén Main Air Blower (MAB) tại Phân xưởng Cracking xúc tác (RFCC) nhằm tiết giảm tiêu thụ hơi cao áp (HPS) tại turbine hơi của MAB cũng là một sáng kiến hay của các kỹ sư BSR. Máy nén MAB được sử dụng để cung cấp không khí đốt cốc trong thiết bị tái sinh xúc tác. Áp suất vận hành bình thường ở đầu ra của MAB là 3kg/cm2g và giá trị cài đặt cảnh báo áp suất thấp là 2,9kg/cm2g.
Dựa trên vận hành thực tế, áp suất đầu ra của MAB được đánh giá có thể duy trì thấp hơn giá trị thiết kế để tiết kiệm năng lượng thông qua việc giảm tiêu thụ hơi nước cao áp. Theo thông lệ vận hành, áp suất đầu ra MAB được duy trì cao hơn áp ở thiết bị sử dụng khoảng 0,5-0,8kg/cm2g để đảm bảo độ mở của van điều khiển trên các nhánh khí ở hạ nguồn nằm trong giới hạn chuẩn.
Đề xuất giảm đầu ra của MAB từ 3kg/cm2g xuống 2,8kg/cm2g đã được phê duyệt từ đầu tháng 6-2015. Từ 30-6-2015, kỹ sư vận hành hiện trường bắt đầu cho giảm áp đầu ra MAB xuống 2,9 kg/cm2g và duy trì ở mức đó 10 ngày. Sau đó tiếp tục giảm còn 2,85kg/cm2g.
Thật bất ngờ, lượng không khí cung cấp cho các đơn vị vẫn được duy trì ở mức cho phép. Ở điều kiện này, độ mở của các van điều khiển trên các nhánh ra của MAB vẫn nằm trong giới hạn vận hành tối ưu (20-80%) của các van. Các thông số tiêu thụ hơi ở turbine hơi MAB giảm. Tính ra lượng hơi HP tiết giảm được là 11.377 tấn. MAN TURBO đã kiểm tra đường đặc tính của MAB và xác nhận điểm vận hành hiện tại của MAB vẫn còn xa ngưỡng cho phép của máy nén.
Theo quan điểm của nhà bản quyền công nghệ Axens (Pháp) cho rằng, không có yêu cầu đặc biệt phải kiểm soát áp suất đầu ra của MAB ở giá trị 3kg/cm2g. Sự vận hành của MAB nói chung và sự cài đặt áp suất đầu ra phải đảm bảo cung cấp đủ lưu lượng và áp suất không khí theo yêu cầu của các đơn vị sử dụng với mức dư hợp lý. Tính đến ngày 21-4-2016 (287 ngày) thì lợi nhuận đạt được là 11.377 tấn HP, ước lượng tương đương khoảng 246.000USD.
Tối ưu hóa công suất vận hành
Năm 2016, một trong những yếu tố thành công là NMLD Dung Quất luôn hoạt động an toàn, ổn định ở 105% công suất thiết kế. Công suất của nhà máy là 6,5 triệu tấn dầu thô nhưng BSR sản xuất khoảng 6,91 triệu tấn sản phẩm, vượt thiết kế 0,41 triệu tấn. Đó là thành quả của 5% công suất vượt.
Kỹ sư Đặng Ngọc Đình Điệp, Phó trưởng phòng Kỹ thuật BSR cho biết: Nếu tăng công suất của Phân xưởng Chưng cất dầu thô (CDU) lên cao hơn so với 100% công suất và điều chỉnh dải công suất của các phân xưởng phía sau một cách phù hợp sẽ giúp tăng thêm lợi nhuận vì khi công suất nhà máy tăng thêm khoảng 10-15% thì các chi phí cố định thay đổi không đáng kể. “Việc thay đổi công suất cao hơn thiết kế đòi hỏi phải tính toán và xem xét giới hạn của các điều kiện vận hành, đánh giá lại toàn bộ các thiết bị, hệ thống. Như vậy, cần phải có nghiên cứu tổng thể nhằm tối ưu công suất nhà máy”.
Nghiên cứu khả năng tối đa công suất NMLD Dung Quất được bắt đầu bằng việc nghiên cứu các dữ liệu như tài liệu thiết kế nhà máy; số liệu vận hành thực tế của nhà máy; kết quả nghiên cứu cho dự án nâng cấp mở rộng nhà máy; tính chất và thành phần dầu thô đưa vào chế biến.
Từ các nghiên cứu ban đầu, BSR đã xác định được giới hạn cho việc tăng công suất của nhà máy nằm ở Phân xưởng CDU. Để đánh giá khả năng tăng công suất của phân xưởng này, một mô hình mô phỏng nhiệt động học đã được xây dựng và sử dụng kết hợp với các số liệu chạy thử nghiệm để đánh giá chi tiết cân bằng vật chất, cân bằng nhiệt cũng như hoạt động của các thiết bị khi công suất phân xưởng tăng lên.
Trong NMLD Dung Quất, hệ thống thiết bị đã được thiết kế với giới hạn dư tối thiểu là 10% (design margin); một số thiết bị quan trọng như quạt thổi khí, máy nén khí… có giới hạn dư lên tới 10-25%. Tuy nhiên, thực tế dầu thô chế biến có sự khác biệt rất lớn so với dầu thô thiết kế (tỷ lệ thành phần các phân đoạn thay đổi lớn theo hướng nhiều phân đoạn khí nhẹ, nhiều phân đoạn naphtha, nhiều DO, ít phân đoạn cặn residue…). Vì vậy, việc đánh giá, nghiên cứu bằng mô hình được thực hiện với 3 loại hỗn hợp dầu khác nhau: Hỗn hợp dầu thô đặc trưng; Hỗn hợp dầu có hiệu suất phân đoạn naphtha cao; Hỗn hợp dầu có hiệu suất phân đoạn DO cao đóng vai trò quan trọng trong việc nghiên cứu tăng công suất nhà máy.
Sự mạnh dạn áp dụng giải pháp này căn cứ vào 2 thực tiễn đã được chứng minh. Căn cứ kết quả nghiên cứu của Hãng JGC (Nhật Bản) cho Dự án nâng cấp mở rộng NMLD Dung Quất cho thấy, khi tăng công suất 10-15% so với giá trị thiết kế, toàn bộ các phân xưởng công nghệ, phụ trợ, ngoại vi đều không đòi hỏi phải cải hoán hoặc yêu cầu cải hoán nhỏ. Ngoài ra, trong khoảng thời gian từ 11-2010 đến 10-2012, NMLD Dung Quất đã vận hành an toàn, ổn định và liên tục ở công suất 105% so với công suất thiết kế với nhiều hỗn hợp dầu thô khác nhau.
Phân xưởng CDU được đánh giá là giới hạn chính khi nâng công suất nhà máy lên 110%. Các kỹ sư đã thực hiện quy trình tăng công suất phân xưởng CDU lần lượt phân tích số liệu; Chạy thử nghiệm ở 100% công suất. Bước tiếp theo là thực hiện chạy thử nghiệm ở 110% công suất. Cuối năm 2013, Phân xưởng CDU được chạy thử nghiệm nâng công suất từ 100 lên 110% với các điều kiện được điều chỉnh nhằm giảm bớt các giới hạn có thể ảnh hưởng đến việc tăng công suất như: Giới hạn công suất bên trong cột chưng cất dầu thô, đặc biệt vùng bơm tuần hoàn LGO và HGO; công suất lò gia nhiệt dầu thô; giới hạn công suất của các bơm tuần hoàn; công suất của tháp ổn định xăng thô, đặc biệt thiết bị tái đun sôi tại đáy tháp. Việc chạy thử nghiệm đã thành công ở 110% công suất, các sản phẩm đều đạt tiêu chuẩn đặt ra, các thiết bị hoạt động trong giới hạn an toàn.
Nhằm xem xét và đánh giá chính xác hoạt động của Phân xưởng CDU trong giai đoạn chạy thử nghiệm, mô hình mô phỏng công nghệ và thiết bị đã được xây dựng và tinh chỉnh theo các thông số vận hành đã thu thập được. Nguyên liệu cho mô phỏng được tổng hợp bằng cách phối trộn các sản phẩm của phân xưởng CDU. Còn đối với dầu thải, do phối trộn với một lượng nhỏ nên tính chất được giả thiết nhằm đảm bảo cân bằng vật chất. Kết quả mô phỏng thu được rất gần với điều kiện thực nên đáng tin cậy khi sử dụng để đánh giá.
Trên cơ sở thông tin từ chạy thử nghiệm ngày 25-12-2014 và trên cơ sở tính toán thực hiện bởi mô phỏng với hỗn hợp dầu thô đặc trưng, có thể xác nhận được từng thiết bị như lò gia nhiệt dầu thô, các thiết bị tĩnh, đĩa trong tháp chưng cất dầu thô, các thiết bị trao đổi nhiệt, các thiết bị làm mát bằng không khí, các thiết bị quay và các thiết bị điều khiển… đều có khả năng vận hành ở 110% công suất.
Tuy nhiên, nhằm tăng độ linh động và sự ổn định cần thiết khi chế biến ở 110% công suất cần có thêm một số cải hoán nhỏ: lắp thêm đường thu hồi khí ở phân xưởng CDU, lắp đặt thêm thiết bị tái đun sôi ở đáy tháp ổn định xăng naphtha T-1107, xem xét thay thế một số van điều khiển có kích thước lớn hơn, xem xét tăng độ nghiêng cánh quạt của các thiết bị làm mát bằng không khí, tăng tần suất làm sạch các thiết bị trao đổi nhiệt để tăng khả năng thu hồi nhiệt cho dầu thô.
Đức Chính - PVN
Relate Threads